The railway industry is undergoing huge levels of innovation across the globe.
Digitalisation is a significant driving force behind the railway revolution; we’re seeing technology and software being used to build a more efficient rail network, improve travel experiences for customers and reduce overall impact on the environment.
Railway maintenance is one such area that’s advancing as the industry continues to leverage digital technologies and ‘smart quality’ is now becoming more commonplace as a result.
Working with Amtrak
FLAGS are proud to be working with Amtrak (also known as The National Railroad Passenger Corporation) in America.
Working in maintenance using our smart quality control software, Amtrak’s engineers are able to visually inspect rolling stock through a real-time dashboard, and mark any issues via visualisations.
By connecting Amtrak’s data and communicating more effectively at every level of production and engineering, they are able to deliver exceptional products that deliver quality, reliability and accuracy.
As digital technology encroaches the rail sector, we’re also seeing digital technologies aid the manufacturing of rolling stock.
What’s interesting is that the rail sector is following in the same footsteps as the automotive sector, where digital twin technologies are now a given throughout the manufacturing process. In the next few years, it wouldn’t be surprising to see digital twins used for the design, manufacturing, and testing of rolling stock in operation.
This virtual, data-driven capability gives engineers the ability to test rolling stock in real-world situations throughout the product lifecycle, from design, through manufacture, and into service.
What is smart quality?
Smart quality utilises software and technology such as IoT (Internet of Things), big data, digital twins, and smart quality control software.
Find out more about the benefits of smart quality control software in manufacturing.
Railway rolling stock
Smart quality doesn’t just enable successful data exchange between rail and infrastructure operators, but helps to improve the design, manufacturing, assembly and testing of rail equipment, including railway rolling stock.
The manufacturing of rolling stock is a time consuming, costly and low volume process that can last for up to three to four years. Production is made up from a series of stages, each one impacting the other. This process then becomes even more complex due to the intricacies, technical difficulties and amount of stakeholders involved.
However, a digital twin can help streamline and speed up this process, as it offers a live, digital representation of the system being developed. Engineers can test systems and gain accurate insights of performance against real-world scenarios.
Predictive maintenance
As a digital twin lasts the course of the product lifecycle, it can gather data throughout the span of rolling stock manufacture and rail infrastructure use, offering invaluable insight into the prediction and identification of components that are at risk of failure or wear and tear.
This invaluable insight means engineers and manufacturers can learn from the data and undertake predictive maintenance, preventing the failures and issues from happening. When engineers and manufacturers use digital twins, they can circumvent cost increases and delays as they’re deriving maximum value from the infrastructure.
How does FLAGS Software support the rail sector?
This is where FLAGS Software comes in. Designed to ensure quality, control, traceability and visibility at every stage of production, engineers and operators can capture and track the data they need throughout the rolling stock manufacturing process, and then through into service and maintenance.
Compatible with both production assembly lines and in-cell manufacturing, FLAGS Software is great for niche manufacturers, as we understand the challenges of delivering high-value products at a low-volume. Through our visual dashboards, we provide a complete track and control process at each cell, including work instruction, checklists, visual inspection and reporting, so that every single product is produced and inspected at the highest level of quality.
FLAGS Software has more than 30 years’ experience in driving improvements in quality, efficiency and cost to the world’s leading manufacturers. By translating processes and records from manual to digital, FLAGS has provided its clients not only with a seamless transition into the use of software in its processes but the benefits of faster, more efficient production. Get in touch with FLAGS today.
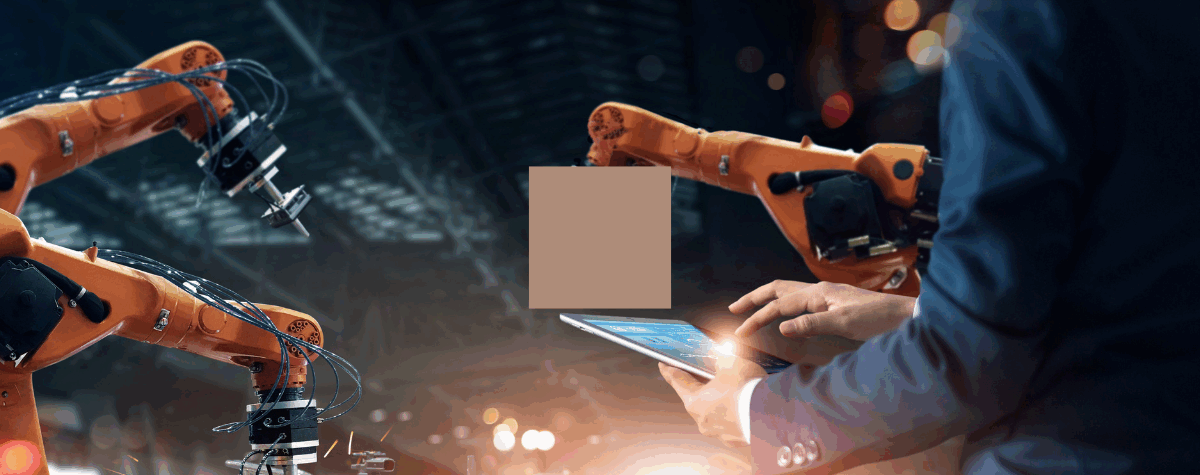
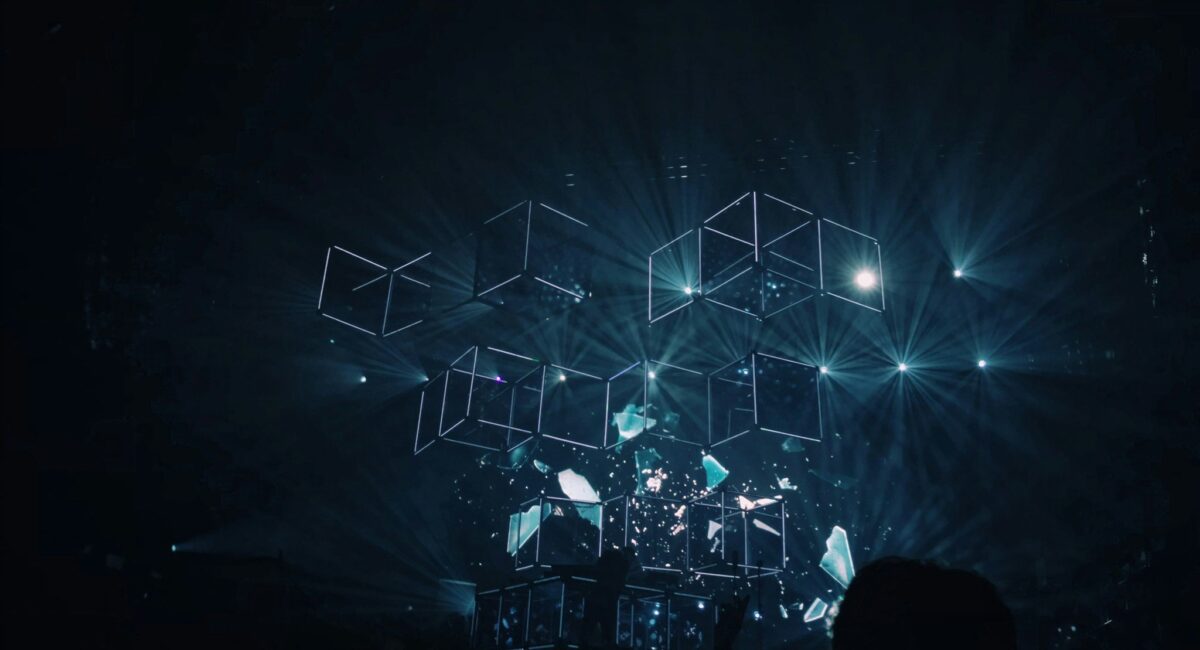
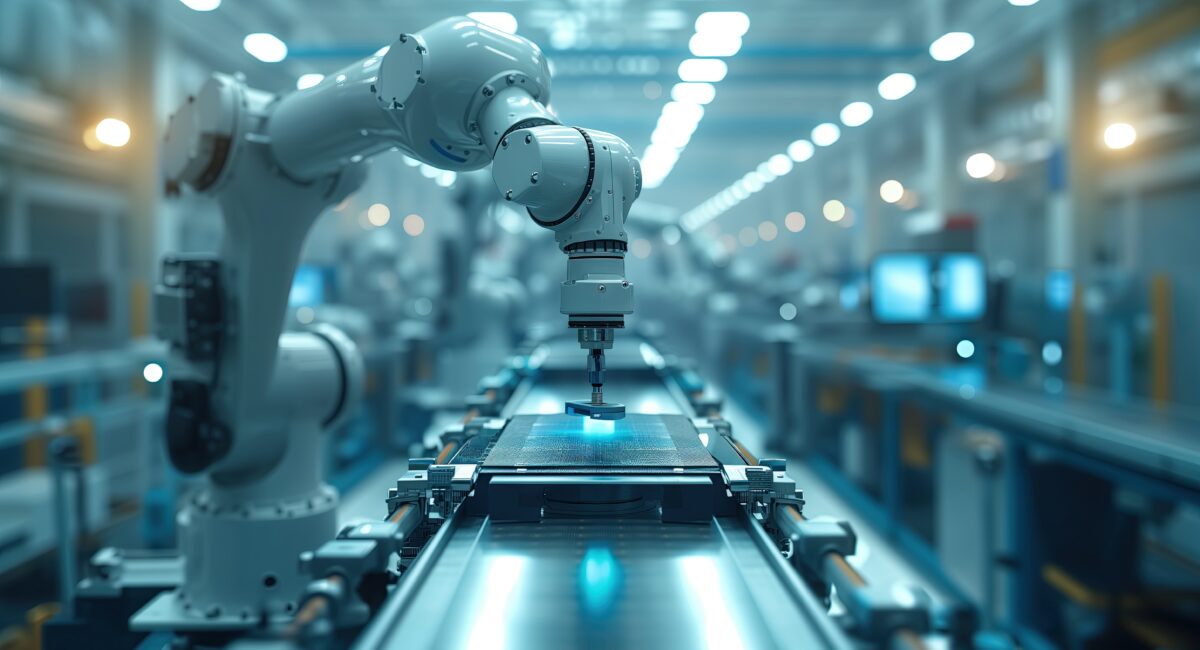