Quality excellence is critical to the success of any manufacturer, no matter how big or small. The relentless pursuit of quality not only strengthens a company’s reputation but also boosts customer satisfaction, loyalty, and overall business success.
But it’s not just the rapid growth of data-driven technologies that’s helping manufacturers uphold these standards. Within this digital revolution, data scientists play a vital role, analysing diverse sets of data to unlock valuable insights.
Their work gives manufacturers the ability to understand how and where they can introduce step changes to drive quality excellence.
At FLAGS, we understand there is great power in combining quality control data with other systems, giving data scientists the tools and insight they need to carry out complex analyses and make data driven decisions that will revolutionise every level of manufacturing moving forward.
The rise of data scientists in manufacturing
Data scientists are instrumental in leveraging the vast amounts of data generated by modern manufacturing processes. With their expertise in statistics, machine learning, and data analysis, they can make sense of complex datasets and identify patterns that can lead to quality improvements. By employing various analytical techniques, data scientists can uncover hidden relationships, detect anomalies, and champion predictive analysis, by spotting potential quality issues before they occur.
The role of quality control software
Quality control software serves as a powerful tool for data scientists in their quest for quality excellence. This software enables seamless data collection, organisation, and analysis, providing data scientists with a centralised platform to perform their work efficiently.
Additionally, the rise of the data warehouse gives data scientists even more granular insight into the manufacturing process, focusing on data that isn’t necessarily production critical but holds key information.
When data scientists can access this information, along with FLAGS data warehouse ( a separate database that can be tapped into without affecting the production process) they can analyse diverse sets of data that will help them identify part shortages, bottlenecks and so much more.
What can data scientists do with FLAGS Software?
Predictive analytics for proactive quality control
Predictive analytics is becoming more commonplace in manufacturing, and it’s easy to see why. Traditional quality control relies on reactive measures to identify and address issues after they occur.
Thanks to FLAGS Software’s real-time reporting functions and numerous data inputs, data scientists can identify any quality issues across the production line, and undertake preventive actions, reducing defects, minimising waste, and improving overall production efficiency.
Real-time monitoring and process optimisation
With the advent of the smart factory, the Internet of Things (IoT) and connected devices, establishing real-time monitoring systems that collects and analyses data from various sensors and equipment is a viable option for manufacturers of all sizes.
When these systems work holistically with existing ERPs and softwares, detailed insights and site wide reporting becomes the norm. FLAGS Software is built on delivering accuracy in information, regardless of the systems it’s integrated with. Real-time data acquisition from the shop floor and assembly lines to quality control and rework stations makes it ideal for tracking improvements and efficiency upgrades across one site, or many.
Quality assurance through machine learning
In the context of manufacturing and quality control, machine learning, a subset of artificial intelligence (AI), can be used to enhance quality assurance by training algorithms on vast amounts of historical data.
This gives data scientists the opportunity to automatically identify defects, classify product variations, and flag potential quality issues. The integration of machine learning algorithms with existing quality control procedures reduces human error, enhances accuracy, and significantly speeds up inspection processes.
Continuous improvement and root cause analysis
FLAGS Software collects and analyses quality data over time, which can help identify recurring issues, uncover root causes, and suggest targeted improvements.
The ability to gain insights from comprehensive datasets empowers manufacturers to make data-driven decisions, prioritise improvement initiatives, and continuously optimise quality control strategies.
When data scientists and manufacturers embrace the power of FLAGS Software, they can revolutionise their approach to quality excellence. By leveraging advanced analytics, predictive modelling, real-time monitoring, machine learning, and continuous improvement techniques, they can empower businesses to identify and address quality issues proactively, optimise processes, and achieve unparalleled levels of quality excellence in manufacturing.
If you’re ready to take the next step toward quality innovation, get in touch with FLAGS Software. Together, we can shape a future where quality excellence becomes the norm rather than the exception in manufacturing.
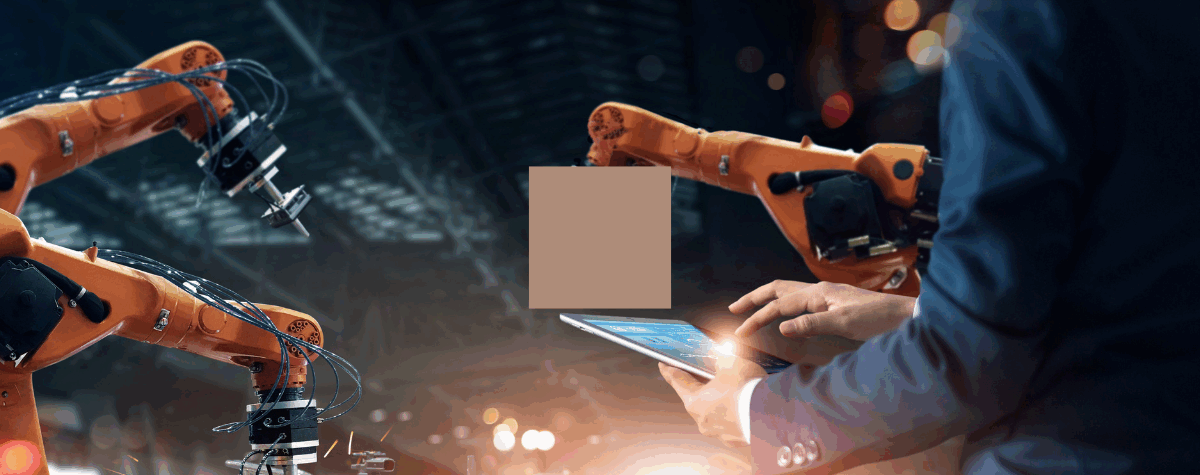
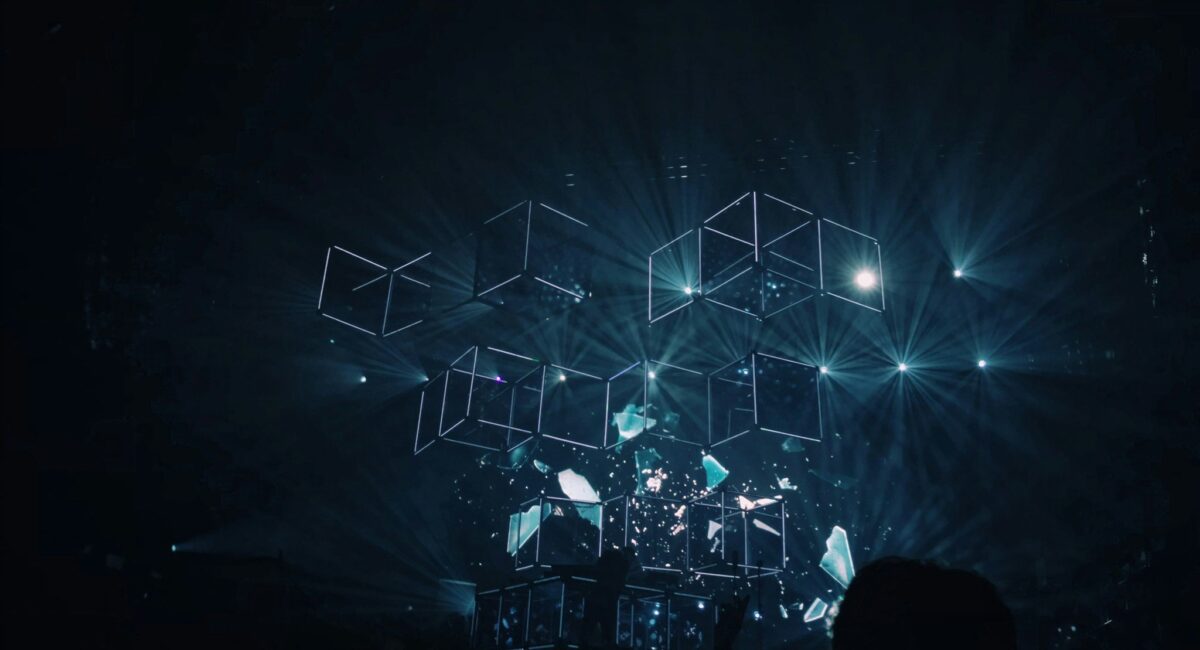
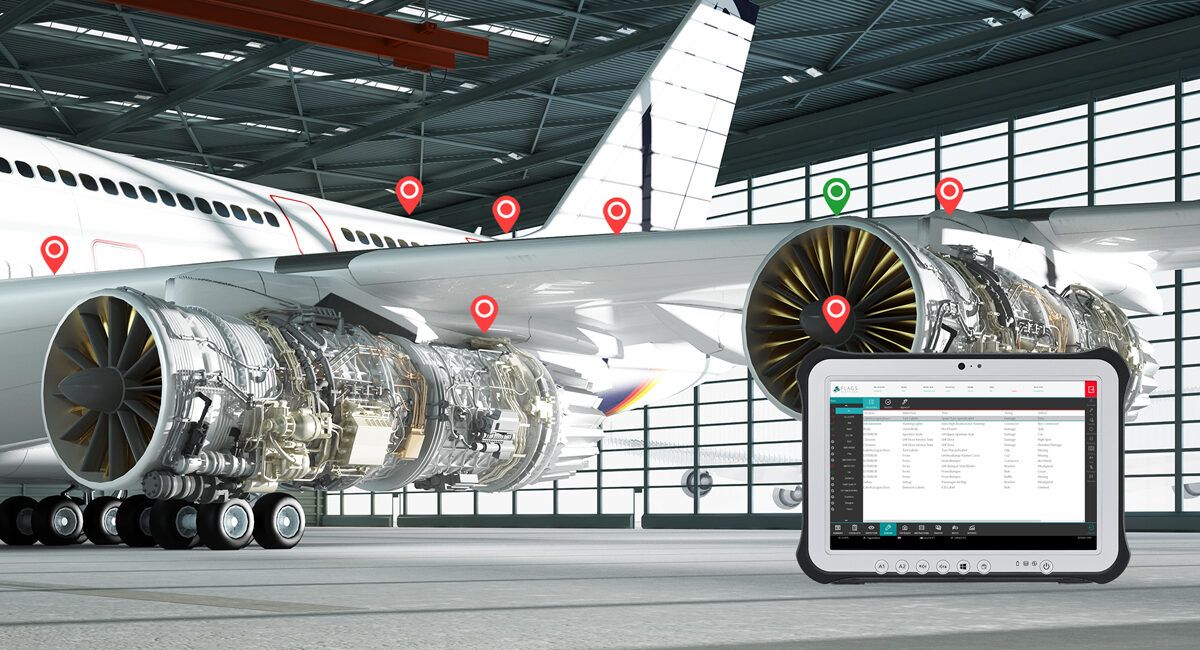