The manufacturing industry is in the midst of a digital revolution, with Industry 4.0 giving companies access to unprecedented levels of data. We’re seeing more automotive manufacturing companies realise the benefits of Industry 4.0, and the quality management process is no exception. System integration, cloud computing and big data are helping revolutionise quality control, and are giving managers invaluable insights on how they can improve their operations and overcome a wealth of challenges.
FLAGS quality management software is renowned for improving production output, enhancing efficiency and giving integrated visibility across several operations. Here are three challenges that FLAGS software is helping the automotive industry overcome.
Reduced emissions and improved sustainability
In conjunction with Industry 4.0, manufacturers are in an era of sustainability, and facing increasing pressure from governments, organisations and customers to ensure their operations are minimising environmental damage.
Quality management software also helps decrease emissions as operations are streamlined minimising the need for rework. Parts and products are made as efficiently as possible, reducing the amount of energy. When quality control managers incorporate FLAGS quality management software, they have access to data that can help automotive manufacturers strive to become Net Zero.
When employees are able to identify any faults there and then, they have the ability to resolve them immediately, rather than at the end of the production line. This also reduces the risk of a customer receiving a faulty vehicle, which will then have to be returned and either repaired or replaced entirely, further impacting the environment.
With FLAGS Software, users can carry out checks via digital checklists and visual inspections, which creates a record and audit. These checks are then visualised in a range of graphs and timelines, with filters that can be toggled to suit each individual check. This gives each station complete traceability, as you can see the root cause of the issue instantly, rather than after a vehicle part has been assembled.
FLAGS Software’s reporting capabilities show you the source of the problem, be it on a specific product, a family of products, a station, or even from parts provided by suppliers.
This helps improve the production process and ultimately remove the cause of the problem, helping to drive down emissions.
Managing many quality control processes
As the UK government looks to phase out the production of petrol and diesel vehicles by 2030, quality control specialists are faced with new challenges when it comes to inspecting parts.
Automotive manufacturers need to ensure their quality control process will scale and adapt to manage the production of traditional vehicles, hybrids and fully electric vehicles.
This means there are many unique quality control checklists for different vehicles and a wealth of data to interpret. Delays or mistakes in analysing this data may mean that issues are overlooked and the necessary actions aren’t taken.
When automotive manufacturers adopt FLAGS quality control software that’s designed for the automotive industry, quality control managers can input data and refer back to digital quality control checklists and visualisations in the form of measles graphs, metro lines, scatter graphs and more, making it much easier to interpret.
This creates a holistic digital history of the parts being produced along with the machines, employees and systems.
Increasing throughput
Throughput plays a vital role in determining the success of automotive manufacturers, and quality control assists in helping organisations meet their throughput targets by producing products Right First Time.
Parts that continuously fail quality checks or flaws that aren’t identified until after a vehicle has been assembled hampers throughput, as it makes it difficult to hit targets and deliver products on time.
FLAGS smart quality software helps automotive manufacturers overcome this challenge by gathering real-time data through digitalised quality checklists, which are then visualised into reports and graphs that can be filtered through multiple data inputs. From this, you then gain insight into throughput, efficiency and more.
This in turn means you can discover any quality issues before the product has even finished being manufactured, and put this right before it gets to the customer.
Find out more about increasing throughput through quality management software here.
Revolutionise your quality control process with FLAGS
Enhance your automotive production and manufacturing processes and achieve a new level of excellence with FLAGS quality management software. Our team of experts have decades of experience helping manufacturers unlock their potential and are waiting to help you do the same. Get in touch with one of the experts at FLAGS today.
Recent Posts
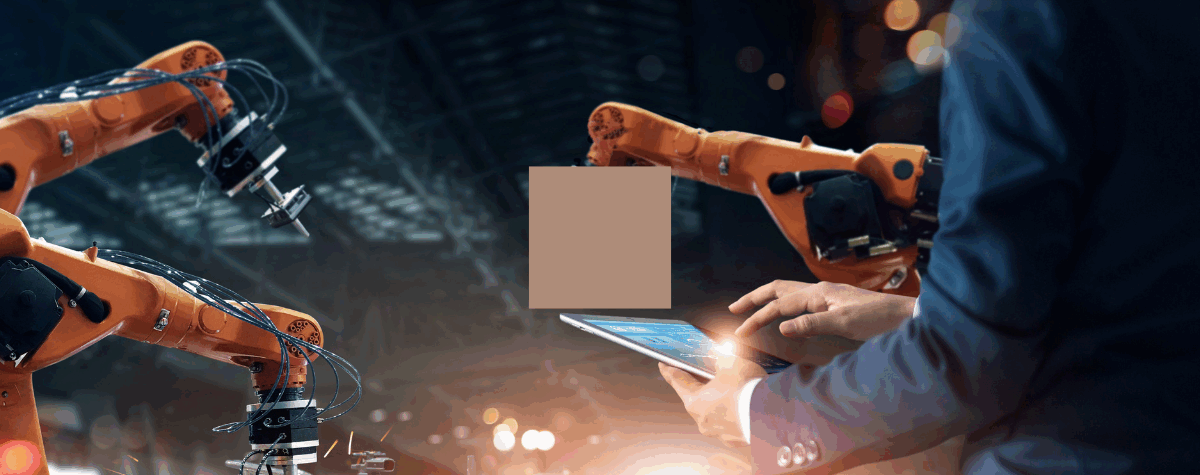
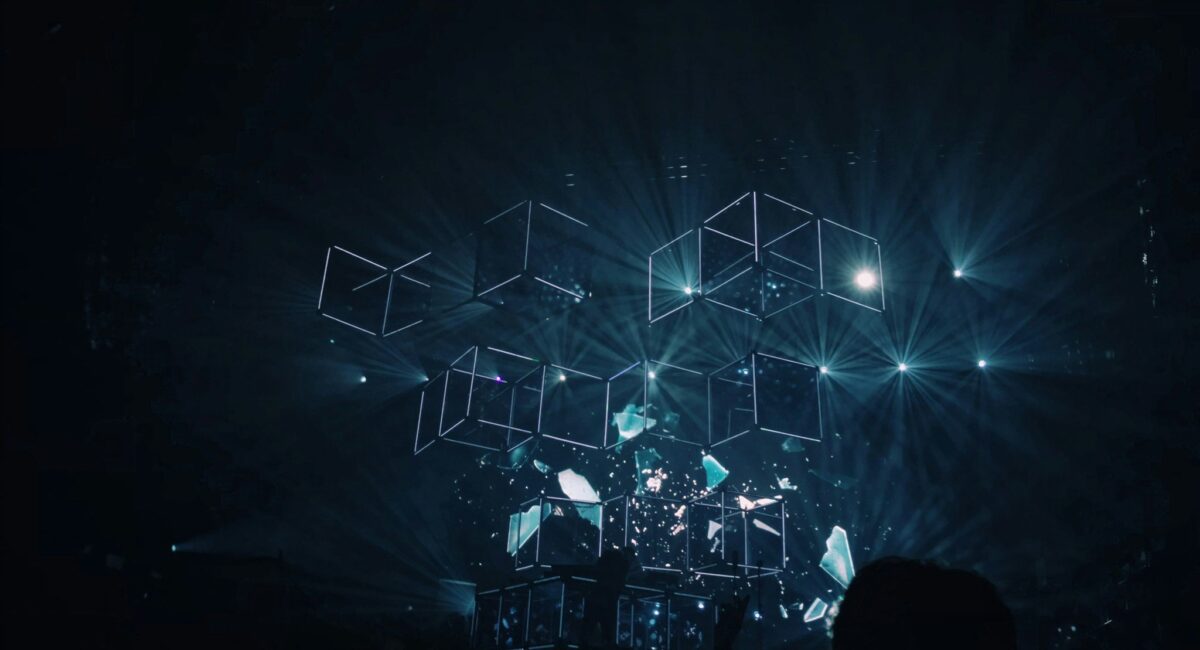
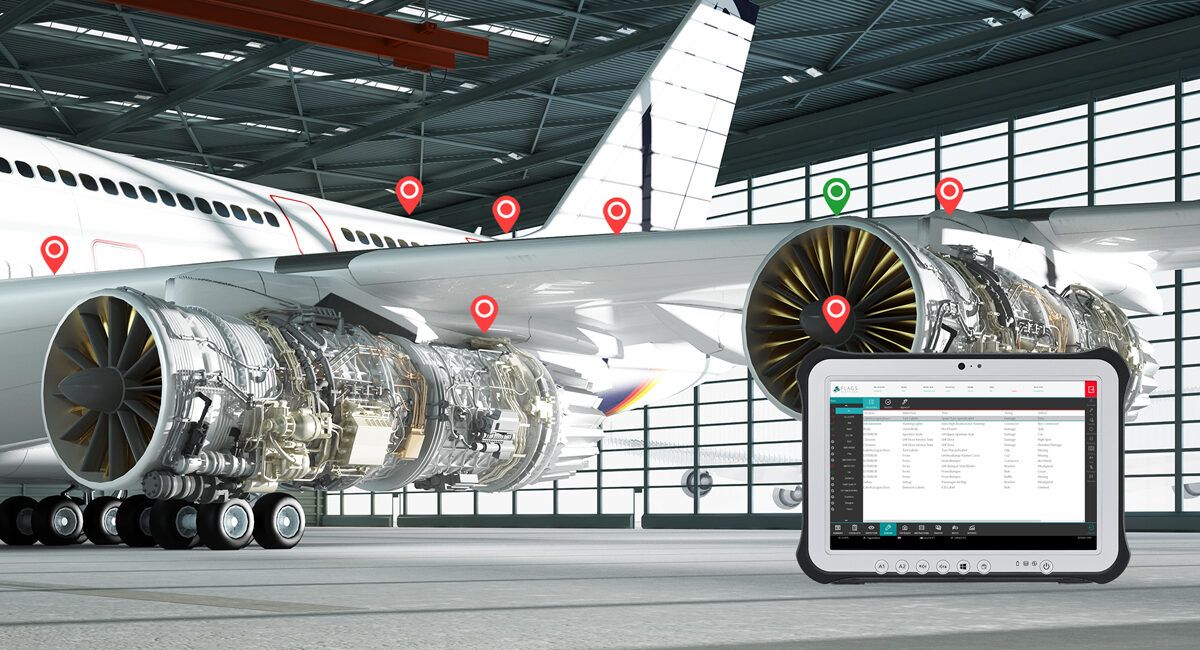