Every manufacturer strives for operational excellence. However, in doing so, they’re faced with the challenge of minimising rework, a critical factor that directly impacts cost efficiency, production timelines and ultimately, customer satisfaction.
As manufacturers embrace smart technology such as the IoT (Internet of Things), AI (Artificial Intelligence), data warehousing and automation, we’re seeing a shift in the production process, particularly when it comes to using quality control to improve overall rework.
The impact of rework in manufacturing
Rework in manufacturing refers to the need to redo or ‘rework’ a part that fails to meet quality control standards or specifications. Rework is a natural part of any production process, but when levels are high, the implications extend beyond additional costs. High levels of rework impact material wastage, extended labour hours, delayed product delivery, and brand reputation.
The traditional approach to mitigating rework has largely centred around reactive measures, which encompasses identifying flaws post-production and rectifying them after the fact. However, this method is both time-consuming and costly. Instead, manufacturers should focus on reducing rework through a proactive strategy that anticipates and addresses potential quality issues before they come to fruition. But the big question is, how?
One way manufacturers can implement proactive quality management is through the integration of AI powered quality control.
Predictive analytics and real-time monitoring
By leveraging historical data, FLAGS, maximising the benefit of AI, can forecast potential production anomalies that could lead to quality issues. This foresight allows for adjustments in the production process, significantly reducing the likelihood of rework.
By analysing vast datasets generated and gathered by FLAGS during the production process, manufacturers can identify patterns and predict potential defects before they escalate into significant issues that require rework. This predictive analysis is instrumental in preemptive problem-solving and ensuring products meet quality standards from the outset.
Alongside predictive analytics, FLAGS in quality control can offer real-time monitoring. Advanced sensors integrated with FLAGS Software work in tandem to continuously oversee the manufacturing process, immediately flagging any deviations from the norm. This instantaneous feedback loop ensures that potential defects are identified and corrected then and there, further minimising the need for rework.
Continuous learning for ongoing improvement
Taking advantage of AI, FLAGS is constantly learning, meaning it continually evolves, becoming more adept at identifying and predicting quality issues over time. This aspect of continuous improvement is critical for maintaining high-quality control standards and further reducing rework rates in manufacturing.
Implementing FLAGS and AI for enhanced quality control
To seamlessly integrate FLAGS and AI for enhanced quality control, manufacturers must have a thorough understanding of the entire production process. This insight is crucial for identifying phases where rework is most frequent or costly. At FLAGS Software, we recognise the importance of pinpointing these pivotal moments in the production cycle and offer solutions tailored to address these specific challenges, significantly enhancing operational efficiency.
The successful deployment of AI technologies, however, hinges not just on the sophistication of the tools themselves but also on the workforce’s ability to adapt to and embrace these innovations. FLAGS Software is committed to facilitating this transition. Our software will be configured to work with your manufacturing model. Our highly experienced team will be there to advise and provide training to equip your team. This ensures that your employees are not just users of technology but active participants in a transformative journey towards smarter quality control measures.
AI-driven quality control with FLAGS Software
As we move forward, it’s clear that integrating AI into manufacturing quality control processes is not just about adopting new technologies; it’s about redefining operational excellence.
We stand at the forefront of this evolution, offering smart quality control solutions that are reshaping the landscape of manufacturing. By partnering with us, you’re not only committing to reducing rework and enhancing efficiency but also to driving sustainable growth and competitiveness in a rapidly evolving market. Speak to FLAGS Software today.
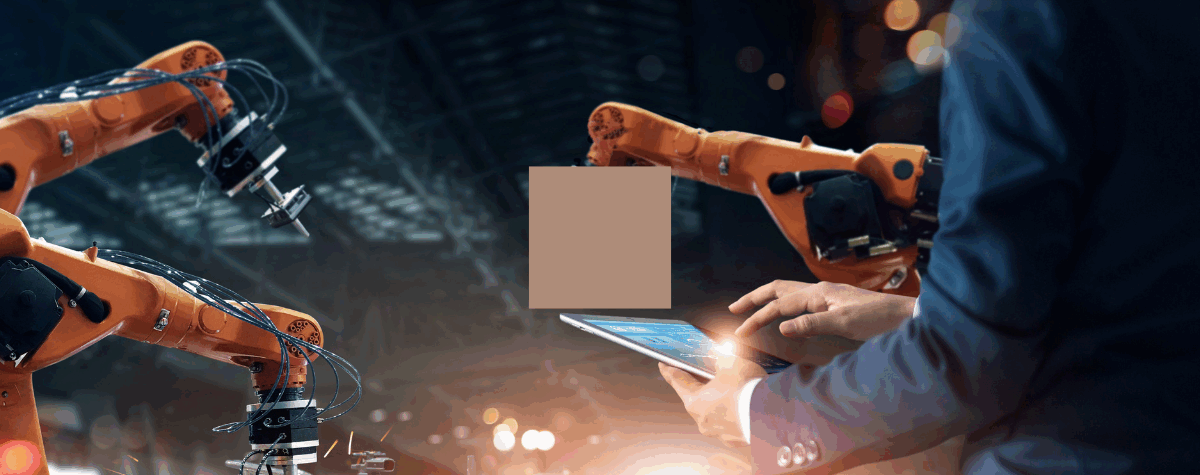
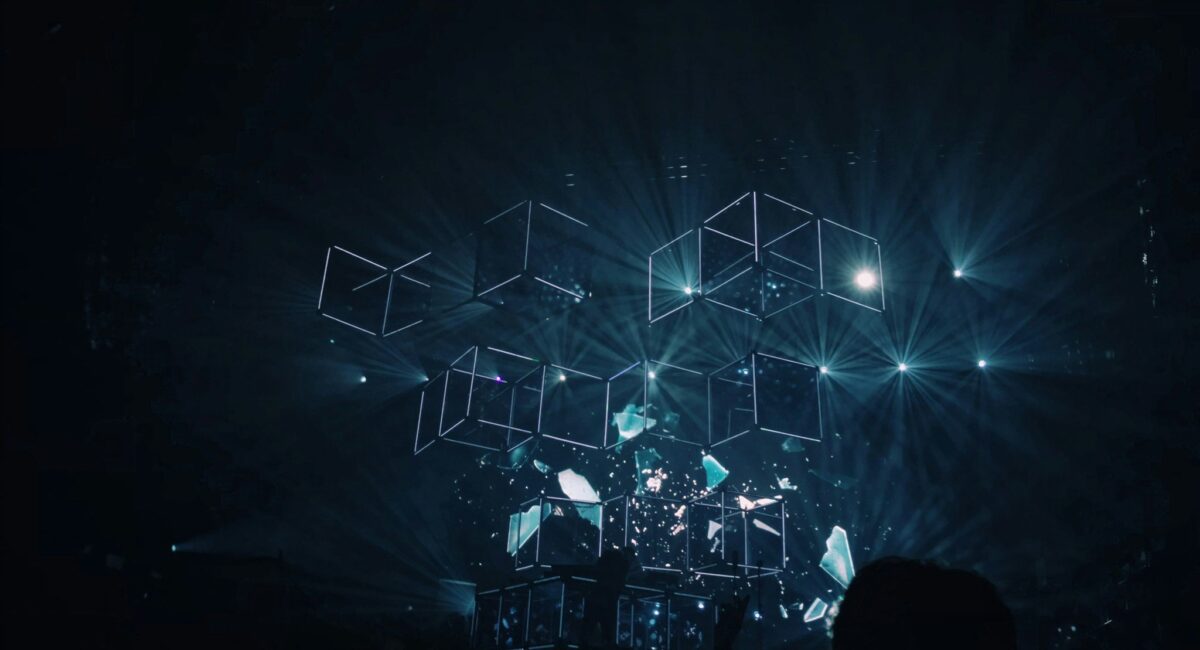
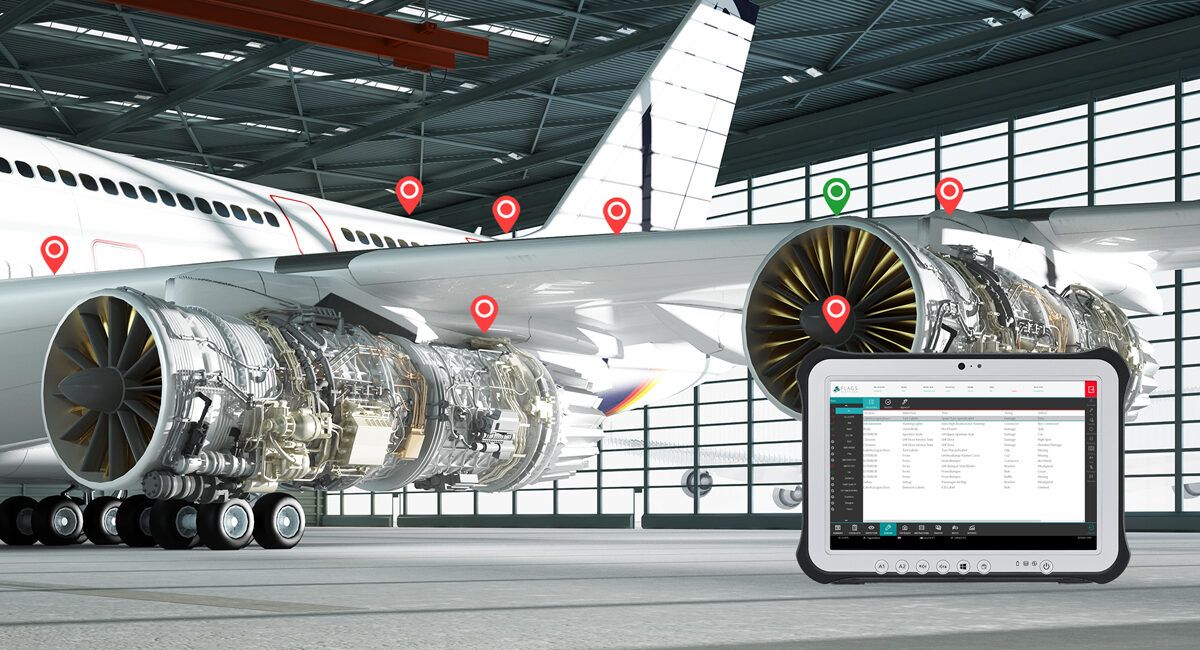