When a part, product or component fails to meet manufacturing standards, they have to be repaired. This process is known as manufacturing rework. Rework is an innate part of the manufacturing process. Whilst manufacturers may have an exceptional quality management system in operation, it’s important to acknowledge that it’s not always feasible to avoid quality issues all the time. This is why it’s crucial to have effective strategies ready to handle such situations.’.
What Causes Rework in Manufacturing?
Even with technological advancements in manufacturing, there are many contributing factors that cause defective, damaged or sub-standard products. This includes:
- Human error
- Machine malfunction
- Faulty materials
- Poorly implemented quality control processes
- Lack of communication between departments
FLAGS will ensure you have the right checks in place to secure the right outcome. Taking your customer order through manufacture, assembly and delivery, we can provide the confidence that you are getting it right first time and avoiding the need for rework.
How to reduce rework in manufacturing
However, when you reduce rework in manufacturing, you can lower your costs of manufacturing, offer a more sustainable business practice, reduce costs in manufacturing and subsequently be more profitable. So, how can operators prevent rework in manufacturing industry? We take you through six integral steps.
1. Track Rework In Manufacturing
If you’re continuously finding that products are going back to rework, it may be indicative of larger problems that need rectifying.
The key to minimising rework and identifying any underlying problems within the manufacturing process is to implement tracking from conception to completion. This, in turn, will give your team the ability to pinpoint exactly where and with whom the issue occurred. You can then identify whether this damage or defect was down to missing elements, damaged parts or human error.
As a result, you’ll have a completely transparent overview of the entire process. From the staff who were on shift at the time of production, to the parts that weren’t working and any other issues, you can identify and fix the weak link in the production line before putting them back into rework, so additional products don’t become compromised by the same issue.
Using FLAGS innovative software, you’ll have complete control, visibility and traceability, allowing you to track each element of production and have a full digital blueprint of each product that is being produced. When a quality issue occurs, the relevant member of the team is notified of the exact location of the issue in real-time, allowing them to act fast and resolve the issue at hand.
2. Review Your Processes
Knowledge is power and data will provide you with the power to make the correct decisions within your manufacturing process, separate data sources (data silos) makes it very difficult to monitor key metrics.
When you review your processes and track your data, you can identify inefficiencies, bottlenecks and issues and then put procedures in place to remove them.
FLAGS Software is built on delivering accuracy in information, regardless of the systems integrated with it. With excellent data collection and collaboration capabilities, FLAGS Software can gather information from a variety of systems. This makes it particularly useful for system and site-wide reporting for truly detailed insights and reporting.
3. Optimise Your Manufacturing Process
When process optimisation is incorporated into manufacturing, they can implement improvements across a wide range of critical areas, which will help to create a more efficient process overall, improve efficiency, reduce costs and minimise rework.
FLAGS Software is designed to acquire data across the manufacturing process from the shop floor and assembly lines to quality control and rework stations, making it ideal for tracking improvements and efficiency upgrades across numerous sites.
4. Leverage Key Technologies
Technological innovation plays a key part in helping manufacturers reduce costs, enhance productivity and decrease rework. From 3D printing to robotics and the Internet of Things (IoT), technology is revolutionising the manufacturing process. If manufacturers want to remain successful, they need to keep improving.
Many manufacturers monitor performance from a physical location – from a site and time management perspective this isn’t the best use of an operator’s time or skillset – this is even more so the case if your processes run 24/7.
When you implement a remote monitoring system that can be monitored from a smartphone or laptop, your operators can review performance on the go. This frees up their time, meaning they can focus on other jobs. This increases resourcing and capacity, whilst reducing overhead costs.
FLAGS Software offers cross platform compatibility and can be used across a wide range of operating systems, from iOS to Windows and Android. This means you can flick between desktop PCs, tablets and mobile phones with ease from any location. It can also be cloud based using a Software as a Service (SaaS) model.
While many companies employ rigorous methods to measure, evaluate, and control, using FLAGS Software can take it to another level – further eliminating issues around quality, consistency of delivery, and improving end-user satisfaction.
5. Embrace predictive analytics
Predictive analytics gives manufacturers and data scientists the capability to use the data from what has gone before to build models that allow predictions to be made of what to expect in the future. This opens up huge possibilities and FLAGS helps to provide this ‘joined-up’ picture.
With FLAGS software manufacturers have access to a complete digital history of the product being made. Rules can be added to promote error prevention behaviour as well as providing the option that a product can only continue in the manufacturing process if quality issues are rectified. This reduces the chances of defective products reaching the market. Find out more about the benefits of predictive analytics in manufacturing.
6. Implement Quality Control
The best manufacturers are defined by their ability to deliver products that never compromise on quality. When operators ensure that their products are consistently made to the right level of specifications, they can reduce the need for rework and get visibility across the entire supply chain.
FLAGS will ensure you have the right checks in place to secure the right outcome. Taking your customer order through manufacture, assembly and delivery, we can provide the confidence that you are getting it right first time and avoiding the need for rework.
FLAGS quality management software
FLAGS Quality Control Software gives you a real time view of the manufacturing process, and ensures that all products are produced to the exact specifications. This removes the need for rework, making your manufacturing process as efficient as possible. All of which is vital in helping to improve cost savings, brand reputation and client relationships.
Reduce the need for rework today with FLAGS Software
FLAGS Software’s team of experts have decades of experience in helping manufacturers reduce rework and optimise their manufacturing processes. We are industry experts. To find out more about our quality control inspection software and how to take your manufacturing processes to a new level of excellence, get in touch today.
Recent Posts
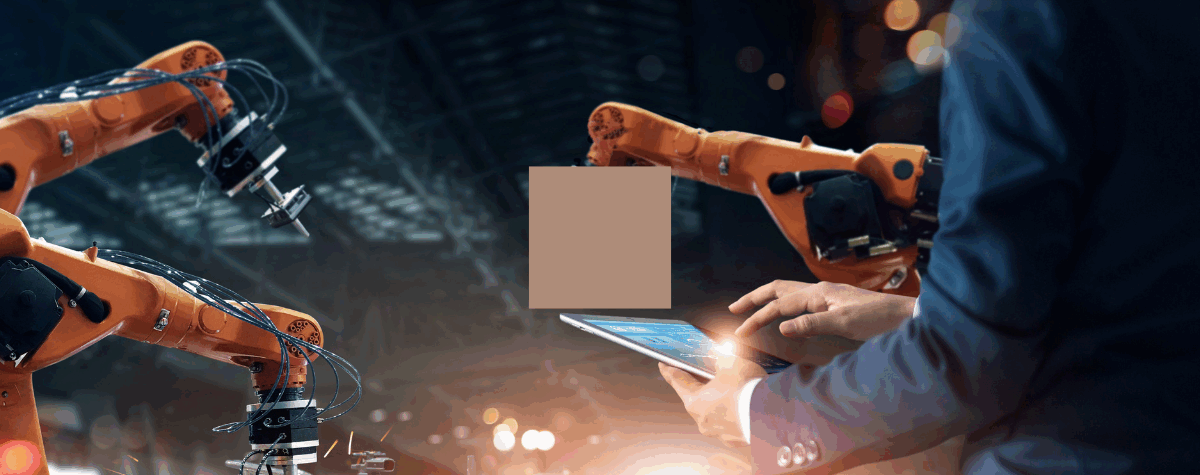
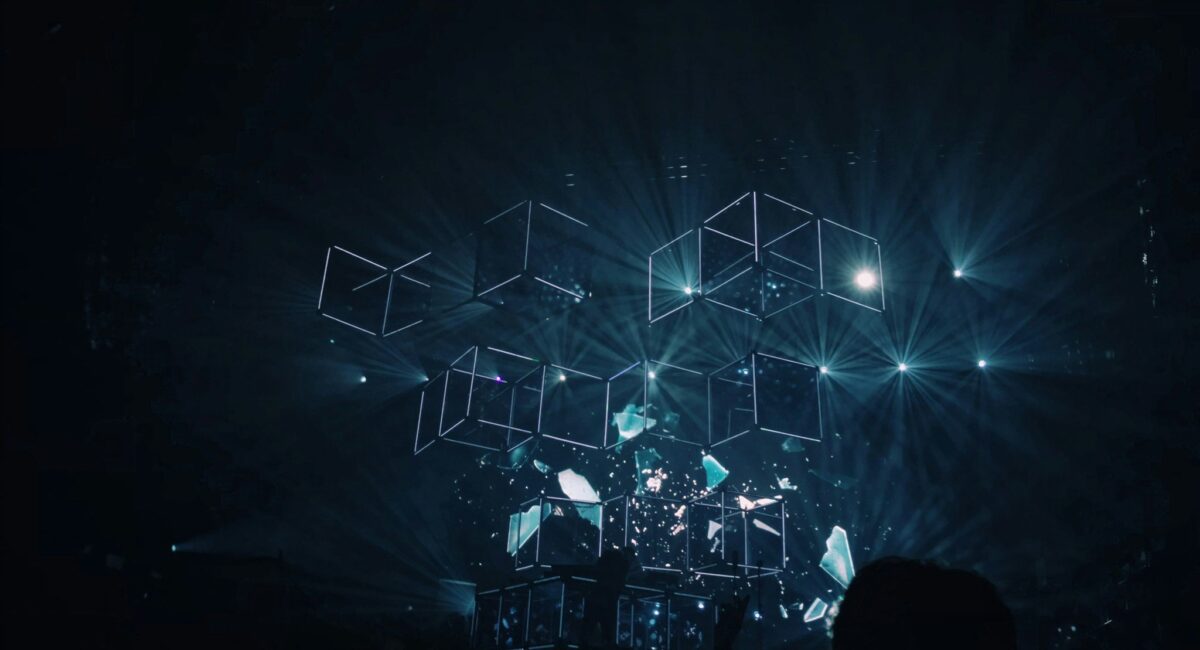
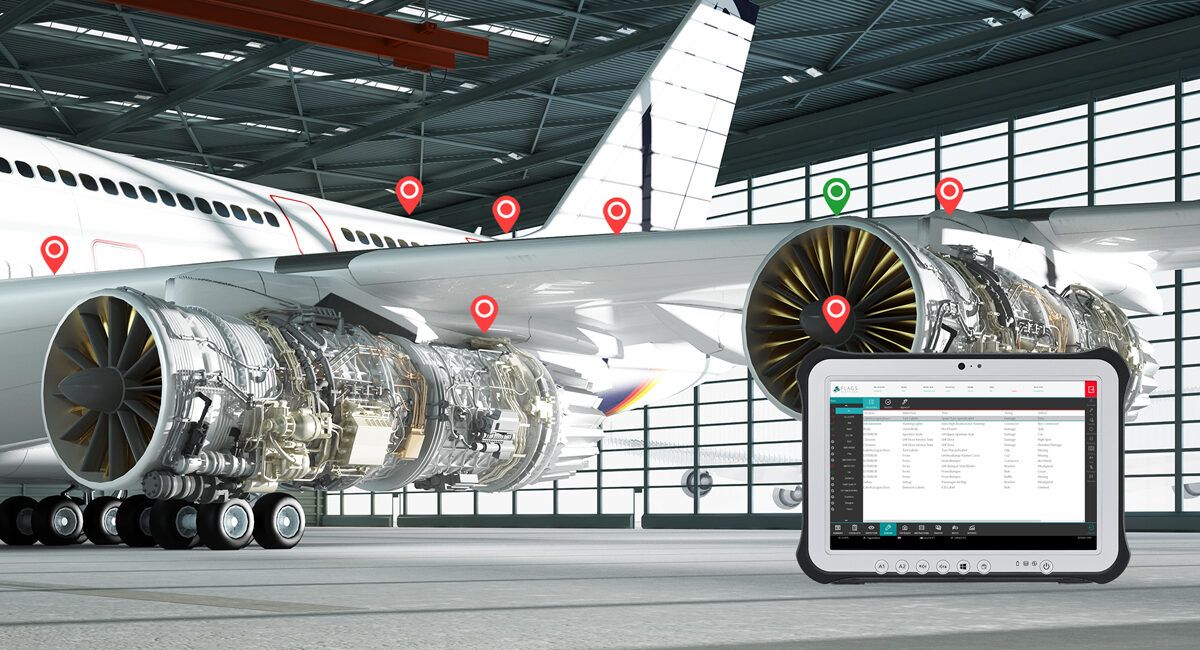