Digital transformation is revolutionising the manufacturing environment, and we’re seeing more and more global manufacturers adopt digital twin technology.
Offering a new level of transparency and efficiency for quality control, digital twin technology isn’t exactly a new technology, but it’s becoming much more accessible for mainstream and niche manufacturers, and not just huge conglomerates with seemingly unlimited resources.
What is a digital twin?
According to IBM, “A digital twin is a virtual representation of an object or system that spans its lifecycle, is updated from real-time data, and uses simulation, machine learning and reasoning to help decision-making.”
To put it simply, a digital twin offers an exact copy of a physical thing, virtually.
The benefits of a digital twin in manufacturing
When implemented properly, manufacturers can do the following:
- Decrease manufacturing costs
- Improve production line and equipment reliability
- Improve overall productivity and efficiency
- Reduce the risk of rework
- Perform predictive maintenance
- Reduce part defects
- Accelerate research and product development
- Increase product lifecycle
How is digital twin technology improving quality control?
Quality assurance plays a vital role in manufacturing, and is critical for industries such as automotive, rail and aerospace. Thanks to artificial intelligence (AI), the Internet of Things (IoT) and other modern technologies, manufacturers are able to use digital twin software as part of their quality management process, and improve it overall.
Speeds up New Product Launch and R&D
In rail, aerospace and automotive, it can take years to design, develop, test and launch a new product or part. It can be months or even years before a part or product is assembled in the production line, due to the sheer amount of research and development.
When manufacturers implement digital twins in their R&D (research and development) processes, products and parts can be virtually tested to understand the following:
- Prospective target audiences
- Geographical markets
- Practical designs
- Potential marketing activity
This gives manufacturers invaluable information from the design phase, ensuring complete product competence, and accelerating the Go To Market plan.
Improves quality assurance
Digital twins are excellent for testing new systems and products, helping with quality assurance. Manufacturers can create virtual prototypes of products, parts and systems and test them against hundreds of variables, including stress tests, weather conditions, temperature changes, paint work, component changes and so much more.
This process significantly saves on cost as the need for physical equipment and extra facilities is reduced, along with the time spent setting up these tests and checks. Through machine learning and data analysis, any issues or gaps in a product’s quality are identified before it moves further down the production line, and Quality Managers can clearly see the source of the issue and resolve it with ease.
Predictive maintenance instead of reactive
As more data and analysis is gathered throughout the quality control process, digital twins can be programmed to predict any areas where quality issues may crop up in the future, giving manufacturers the ability to be proactive.
Digital twins can be used to simulate several different scenarios and predict their outcomes, which means manufacturers can identify any issues in their production process and resolve them before the process itself is implemented in the physical production process.
Data on machine performance and product quality is continuously collected throughout the production lifecycle, which means manufacturers can produce better products at lower costs. With this near-real time lifecycle view, digital twin technology can spot trends and patterns, and give early warning alerts about potential product issues or machine breakdowns before it happens. This helps avoid the costs associated with reactive maintenance.
Improving manufacturing efficiency
Digital twins can be used to optimise the overall manufacturing process, as well as quality control management. When paired with machine learning and data analysis, manufacturers can get a clear picture of the entire manufacturing process from start to finish, and identify any bottlenecks and weaknesses, all of which can be improved.
When each part of the manufacturing process is reviewed, waste is reduced and yields are increased, which aids scalability and overall efficiency.
Answering key questions
Digital twin technology’s uses exceed far beyond design, testing and product lifecycle. Through machine learning and data analysis, manufacturers can get answers to business critical questions, such as how a part will perform under different conditions and stresses. This means manufacturers can gain valuable insight on how parts react individually and together, impacting future operations.
How is FLAGS pioneering digital twin technology?
At FLAGS Software, we’re trialling digital twin technology with our quality management software across a wide range of industries, including automotive and rail. Used at every stage of the manufacturing process, quality managers can optimum quality control and close the feedback loop.
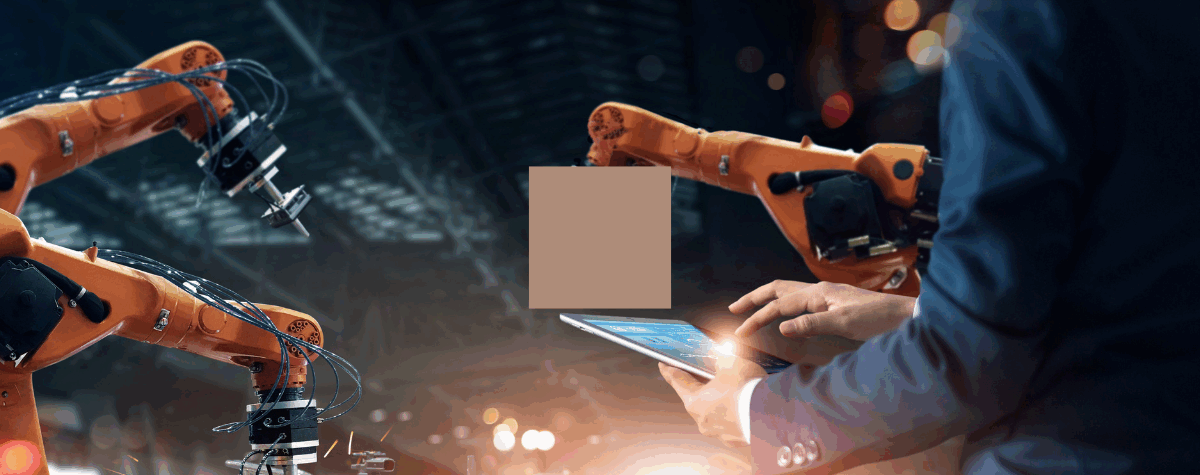
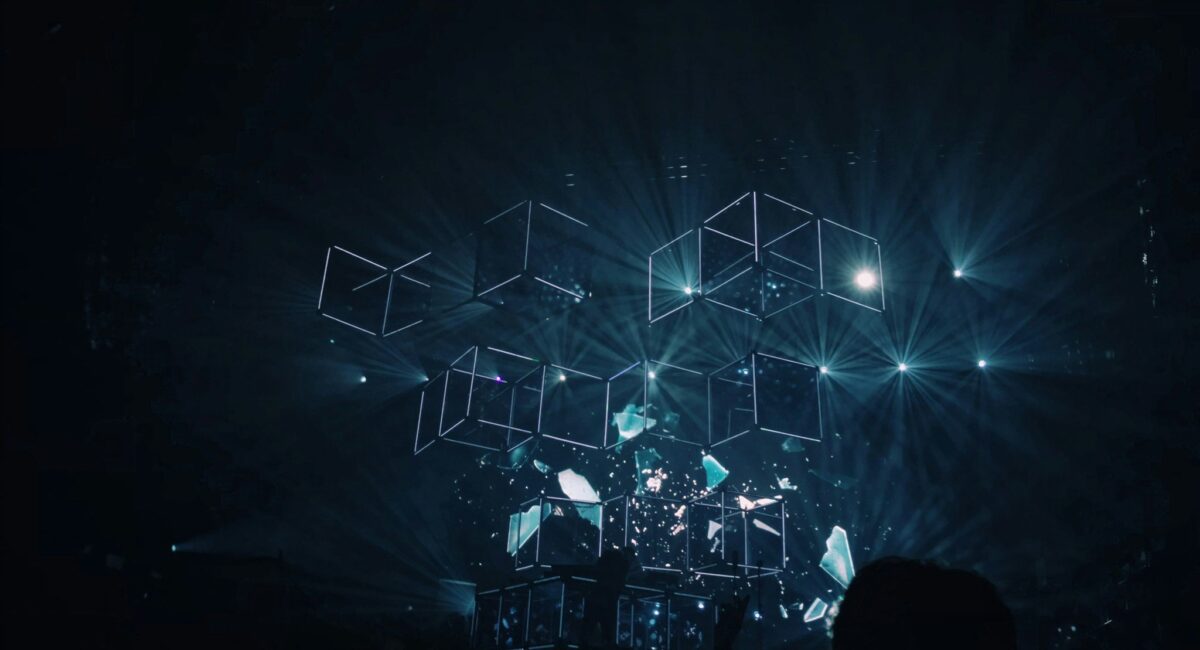
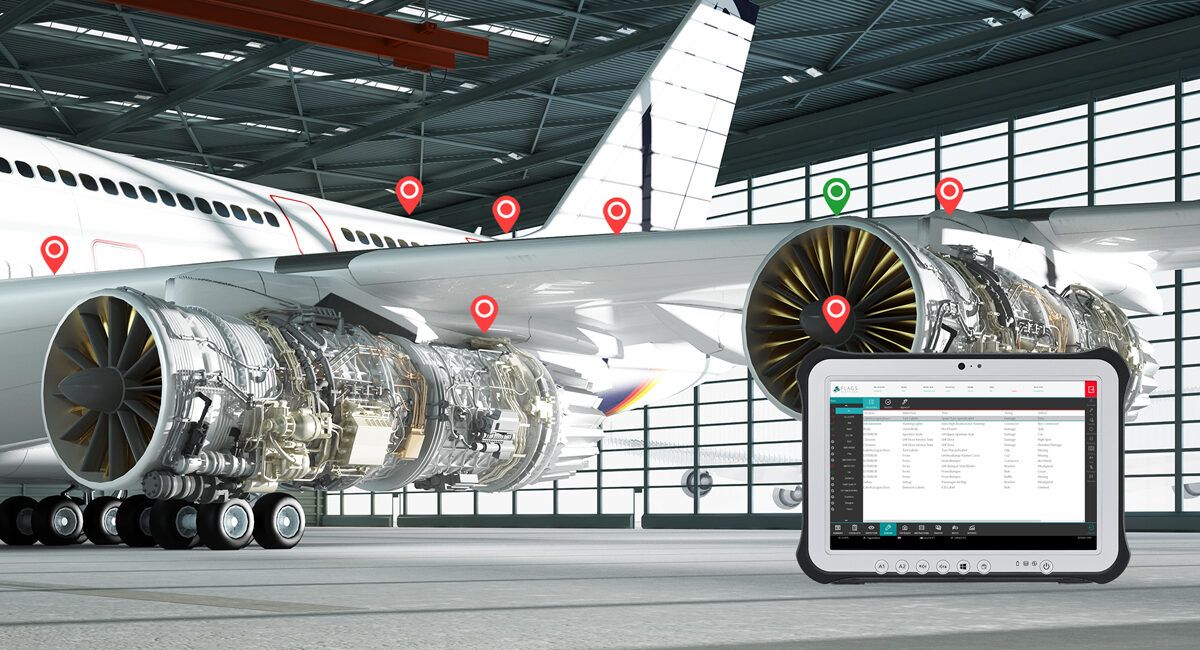