When quality management and LEAN Manufacturing initiatives are brought together, productivity and efficiency is maximised and waste is drastically reduced.
The LEAN Manufacturing philosophy is made up of three parts; Business Value Added (BVA), Customer Added Value (CAV) and waste.
If a process, task or activity doesn’t bring value to the customer or business it is defined as waste. In LEAN Manufacturing there are seven types of waste which are categorised as: Overproduction, inventory, motion, defect, over-processing, waiting and transport.
When manufacturers integrate FLAGS real-time manufacturing tracking software, this waste can be reduced.
Through real-time reporting and analytics dashboards, quality control managers get a clear view of workflow performance and target status.
With this information, manufacturers can identify and rectify any inefficiencies, ensuring productivity is streamlined. Here are the areas in which FLAGS can support:
Overproduction waste
Overproduction is one of the biggest and most serious of wastes as it influences all the other types of waste. Overproduction can lead to a surplus in inventory and stock holding, which incurs costs including capital tied up in inventory, excess use of raw materials, and if the product is produced before it’s needed, it may become broken or obsolete, resulting in environmental issues and even more waste.
With FLAGS Work In Process (WIP) reports, manufacturers get a clear picture of production and inventory, which means manufacturers can fine tune the production process, ensuring only the necessary parts are produced.
Inventory waste
Inventory waste is often impacted by overproduction and poor stock management and encompasses any unprocessed inventory, including the transport needed to move inventory to the storage units, and energy used in storage spaces. All of this also hides original wastes that come with producing inventory.
Additionally, storing stock for an extended period of time can result in damage and deterioration of stock, resulting in more materials and parts needed to replace broken inventory, adding to the never ending cycle of inventory waste.
However, FLAGS is designed to integrate with existing business systems and gathers data from the very start of the manufacturing process straight through to the shop floor and assembly lines. Our smart quality control software gives managers a clear view of assembly steps, providing production with accurate information and easy to read interfaces.
Motion waste
Motion waste refers to any unnecessary movement from a person, piece of equipment, or product that isn’t needed. From a worker reaching over to pick something up, to excess materials or energy being used or wear and tear on machines, any motion that’s deemed unnecessary resulting in capital deprecation must be streamlined.
When Quality Control Managers implement FLAGS Software, they get insight into the production process from start to finish, and are able to analyse and reduce any motion waste.
The reporting feature has the ability to gather data throughout every stage of production and manufacturing processes. By harnessing the power of data in real-time reporting functions, interactive smart dashboards and multiple data inputs, FLAGS Software offers precision, identifying any quality issues across the production line, helping organisations achieve the next level of quality, efficiency, and control.
Defect waste
If a product or part deviates, is substandard, deviates from the original design or is damaged or marked during production, it is deemed as defective and must be reworked or replaced.
Defective waste also encompasses the human labour and paperwork that goes into processing defective parts and the resources needed to put it right.
FLAGS Quality Management Software helps manufacturers ensure their manufacturing processes are working to deliver value, quality and great final products, reducing the need for rework and optimising overall processes.
Shopfloor users are able to record quality issues that are identified during manufacturing and record them through visual defect mapping.
With a smart interactive dashboard using colour coded statuses, easy to review graphs, and performance tracking charts and percentages, it’s easier than ever to get feedback on data.
This provides traceability and a complete digital history of the product being made. Rules can be added to promote error prevention behaviour as well as providing the option to hold a product during the manufacturing process until quality issues are rectified.
Over-processing waste
From painting a part that won’t be seen, to adding unnecessary features that won’t be used, over-processing encompasses anything that adds more value than is needed or wanted. Over-processing waste results in excess materials, energy being used, and extra labour and man hours.
Waiting waste
Waiting waste refers to any time wasted due to down time, broken machinery or production lines being halted. For example, if one process in the production line takes longer than the others, and employees are waiting to move onto the next task, or there aren’t enough employees and a part is waiting at a station for an employee, then time (wait) is wasted.
In order to combat this, workflow must be streamlined and better coordinated. Otherwise, there is risk of products being poorly manufactured or taking longer to produce due to inefficient workflow.
Transport waste
Materials and products need to be transported, but it’s important to ensure time and costs associated with transport are minimised. This includes having facilities that are close to each other, including suppliers, and implementing more efficient methods of transport.
For manufacturers looking to make their production more sustainable, looking at how they can implement waste management is key.
From excessive use of raw materials and consumption of energy, to time lost during the production process, as manufacturers look to make their processes more sustainable, FLAGS Software can help them streamline processes, reduce rework and ultimately become more profitable.
FLAGS Software’s team of experts have decades of experience in helping manufacturers reduce waste, enhance productivity and optimise their manufacturing processes.
We are industry experts. To find out more about our quality control inspection software and how to take your manufacturing processes to a new level of excellence. Get in touch today.
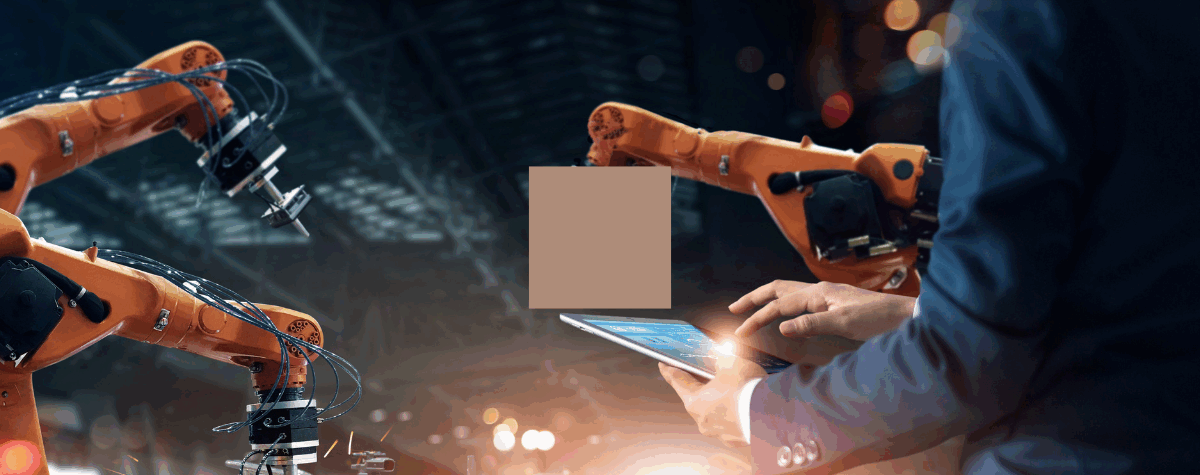
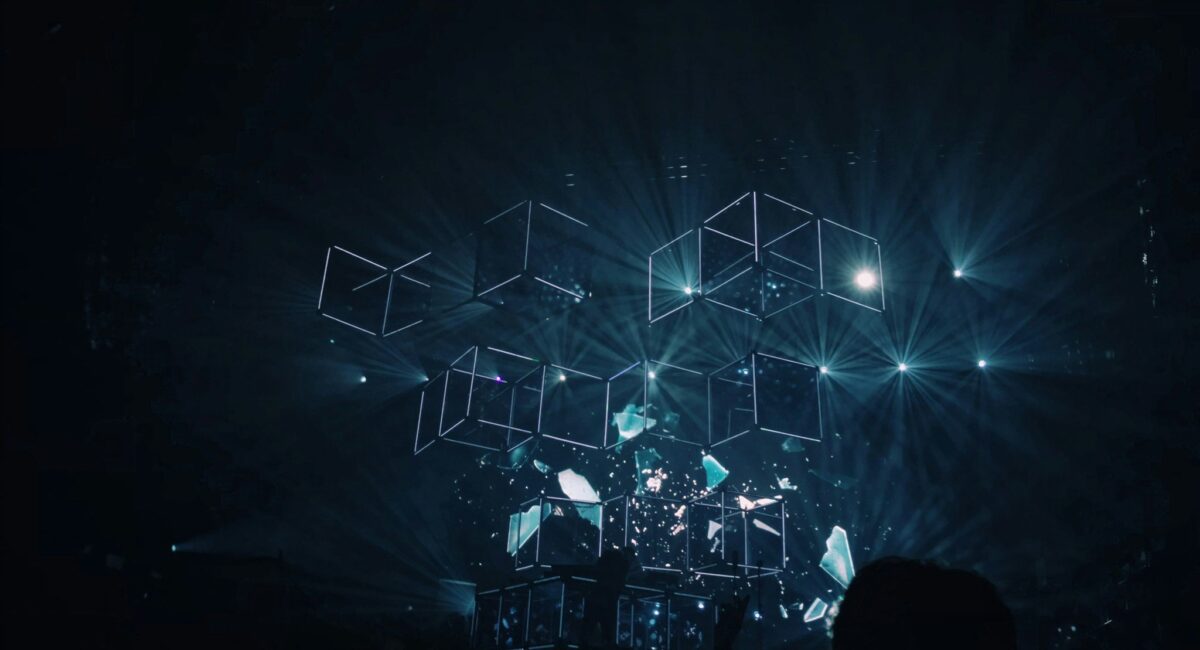
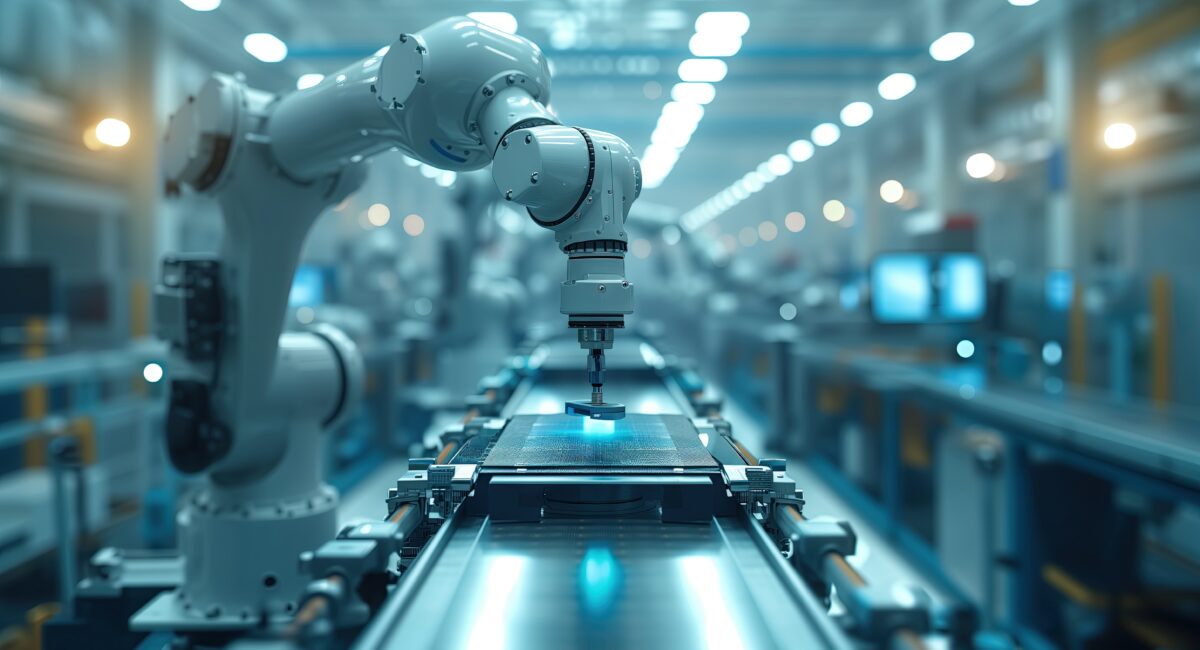